We are still making progress and this report will outline what has happened since the last report on January 20.
General Statement
A bit of context is necessary here. The first machine continues to perform well. There are problems that were anticipated that we are dealing with. One of the overall reliability issues is that many electronic parts in the machine are customer Ampex hybrid circuits that are obviously not available anymore. Figure 1 shows what we have done to overcome this:
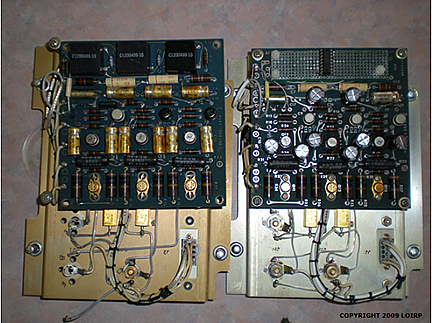
Figure 1: Capstan Motor Driver Assembly Before (left) and After (right) Modifications. Copyright 2009 LOIRP reproduction or republication prohibited without prior written permission.
Using chip technology from the 70’s that are still available, along with modern capacitors we have updated the motor drivers and made the circuits timing more consistent, resulting in a more stable motor drive system. We are going to do this in other areas of the electronics for the analog amplifiers for the signals and generally improve the signal system.
We are continuing to deal with old age related electronic failures as circuits that have not been operational for decades age and fail more rapidly. When this happens there are many reasons and we have typically just done wholesale replacements of parts that are similar and who are known (by Ken who has a great feel for circuit reliability) to fail for age related reasons (germanium transistors, electrolytic capacitors for example).
All in all the first machine is working fine and we are moving to bring the second back to full operational status. Following are details on the status of various refurbishments that are going on.
Heads
We now have had delivered to us our first refurbished head by VMI with a second in process. Figure 2 shows the refurbished head:
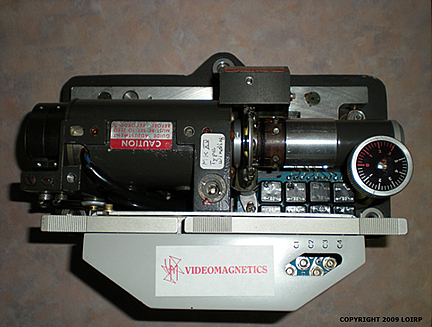
Figure 2: Ampex FR-900 Head Refurbished by VMI. Copyright 2009 LOIRP reproduction or republication prohibited without prior written permission.
This refurbished head qualifies the process that VMI, in consultation with us, have developed for the refurbishment of further heads. The process is a bit constrained relative to the work that is done to refurbish commercial heads. The bearings on the heads are not replaced, which is slightly worrisome to us, but at this time there is greater risk involved with replacing them as there are no procedures for doing so and VMI has limited capabilities to do so. Out of the sixteen heads that we currently own we have 11 that we feel are possible candidates for refurbishment without bearing replacement. Since we at worst case only need four heads to complete the digitization of the entire Lunar Orbiter collection, we feel that the risk is small.
We have one other head that was a test of the process whereby the windings on the head were different than standard, which turned out not to be workable (the head that was delivered was wound this way and VMI simply rewound the new head in the same way), and there is no information on why the head was originally wound that way. This will be corrected and we will send this head back to be wound in the way that we know works. Figure 3 is Lalo Zanetta checking the refurbished head on the drive.
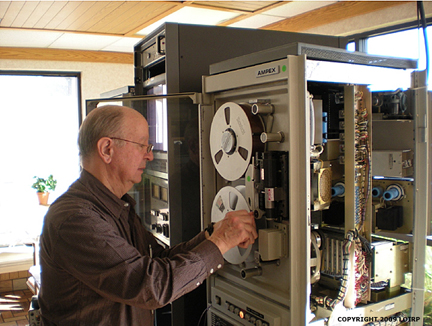
Figure 3: Lalo Zanetta from VMI Checking Head Guide Alignment on the Drive. Copyright 2009 LOIRP reproduction or republication prohibited without prior written permission.
The bottom line is that we now have a proven process for head refurbishment and consider that this milestone has been achieved. More photos on the facebook group.
Motors
We are closing in on this milestone. George Athan, of Athan corp has completed the physical refurbishment process and we are ready to move into the testing phase. George came by this morning to pick up a Motor Driver Assembly (MDA) that we rebuilt from one of the spare parts machine so that he can run and make sure that the motors are properly balanced. This is a key milestone and deliverable that we will have accomplished in the next week.
One note here is that we are very fortunate to have the two extra drives that are our parts donor machines. One of the problems that we have for both the heads and the motors is that there is no test equipment for them anymore. What we have done is taken subassemblies and circuits from the parts donor machines, refurbished them, and then turned them into test fixtures for the heads and motors. This has saved us a lot of time and money to do so.
FR 901 Second Drive
We are making slow progress with the second drive. We have replaced most of the capacitors that we needed to replace but we stopped testing the complete unit when George from Athan Corp asked for the Capstan motor so that he could see what a fully assembled motor looked like in order to compare and make sure that he was reassembling the other two motors correctly. Without test procedures (for which the documentation no longer exists), this is the best way to make sure that the motor goes back together properly. We are fortunate in that Athan Corp has been doing this type of work for 20 years and George is relying on his many years worth of experience on similar motors and equipment as a guide to refurbishing ours. We should have refurbished capstan motors for both units (FR-900 and the 901) back next week. A lot of the design improvements that we have been doing will be integrated into the FR-901 and will speed the process of bringing that drive to life.
Software
Progress continues to be made in software. Gordon Woodcock has substantially completed the work for the automated assembly of framelets. I took a disk drive full of data and Gordon has been able to work with that. The goal is to allow us to fully capture an entire image without stopping and starting the drive and then allow the data to be read in chunks from a several gigabyte file. This will allow us to considerably improve our productivity during the production process.
Demodulator
The final, yet key task that we have to accomplish before moving to production, is the recreation of the demodulator. We have hit a snag in that the stability needed in the demodulator is such that it requires a filter with a bandwith of one hertz. This is an incredibly narrow filter that also can’t drift, therefore the only way to do it is with a crystal filter. This also required some design changes to the demodulator to accommodate this filter design. Our team engineer Al Sturm has ordered the appropriate crystal and it is going to take two weeks to build, test, and integrate into the demodulator design. We expect now to have the demodulator back to test around the 16th.
With the demodulator working we will be able to rapidly begin to create new images. The funding for this was not provided but we can reach this final milestone to complete the refurbishment, get some images out, and be ready for the production phase for getting all the images done.
Respectfully Submitted
Dennis Wingo
LOIRP Project Lead
I just saw info on your project from a friend on the Ampex mailing list…. we may have some FR-900 parts left over here at Langley from years of using them for radarscope recording. I know I have a box of 2″ tapes kicking around but I think the
spare head stacks hit the dumpsters a couple years ago when the Wyle Labs office was shut down. I may have some guides and the alignment tools, though.
Hi, Dennis, Ken and team…
The folks on the Quad Videotape Group list are following your activities with interest.
So are many others as members of the Association of Moving Image Archivists.
Good luck with the demod circuit.
If any of you are at NAB on Tuesday, please hit the Second Annual Quad Videotape Group lunch. Dennis is on the QuadList and should be getting details.
Again, congratulations on the successful work!
Ted
Secretary
Quad Videotape Group
I used to work on Ampex machines (branded as RCA at the time)around 1968/1969. From what I can remember, those air bearings were crap and getting even 50 hours from them before rebuild was a challenge. Most of the time you could get 200-250 hours but each head had its own life span and it varied greatly. Good luck.
Many thanks for great work!
andrea
IK0MMI
Italy
I was the systems engineer at the Goldstone tracking site for the LO program where a lot of those tapes were made.
If I can be of any help let me know.
Richard H. Kelly